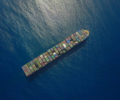
Hull coatings are often over-looked when developing sustainability agendas, but the carbon-cutting advantages of advanced biofouling technologies can take you a long way in lowering GHG emissions.
The most recent International Maritime Organization (IMO) Marine Environment Protection Committee (MEPC76) meeting in June moves shipping ever closer to a significantly reduced-carbon future. It forces ship operators and owners of vessels over 400 gt to analyse their vessels’ output and ultimately find ways to bring their carbon emissions to an acceptable level.
Due to come into force on 1 January 2023, owners and operators will be required to calculate their energy efficiency ratings through the Energy Efficiency Existing Ship Index (EEXI) and establish their annual operational carbon intensity indicator (CII) and CII rating, with A being the highest score. IMO is encouraging ports, administrations and other stakeholders to offer incentives for the highest performing ships, whilst those with a score of D or E for three consecutive years will be required to submit a corrective action plan to their classification society.
These regulations are in line IMO’s commitment to reducing shipping’s total annual greenhouse gas emissions by at least 50% by 2050 compared to 2008. Such regulations are designed to keep maritime sustainable in the long-term and to build a fair playing field for the industry as a whole. And when considering carbon reduction, every aspect of a ship’s operations should be considered, including its hull coatings.
IMO’s GloMEEP (Global Maritime Energy Efficiency Partnerships) says: “The savings of applying advanced hull coatings is difficult to measure, but there is no doubt a possible saving by applying high end products.” With the right coating solutions, these savings, which are not just ‘possible’, but rather proven, are realised through reduced fuel consumption, which in turn results in fewer emissions, and these reductions should not be underestimated.
Performance is key
Hull performance remains a crucial element in understanding fuel performance, regardless of vessel type. Vessels may have longer voyages with higher speed and activity, or less predictable patterns with slower speed and more idling. In both cases, hull performance has a big impact on fuel used. For this reason Hempel developed its SHAPE methodology to help its customers monitor their hull/ fuel consumption dynamic.
Speed loss is a critical measure for understanding vessel performance and fuel efficiency since power increase and speed loss are directly related. Defined by ISO 19030-1:2016, which is concerned with ships and marine technology – measurement of changes in hull and propeller performance, the programme is able both to monitor long term trends via the in-service performance KPI, and also short-term trends through the maintenance trigger KPI. This adds value to vessels with low activity, generating data to understand how much the hull is affected by long idle times, allowing owners and operators to make fact-based decisions.
Futureproofing customers’ assets
Hempel’s Hempaguard X7 coating is proven to beneficially affect both the EEXI- as well as the CII-rating.
The EEXI-rating will improve by 2 per cent thanks to the superior smoothness of Hempaguard X7. This 2 per cent EEXI-improvement translates into a 6 per cent fuel reduction directly after the coating has been applied (using the rule of thumb of a 1:3 relationship between speed and power/fuel).
The CII-rating is influenced by how energy efficiently the ship is operated but also highly dependent upon how well the hull coating can prevent marine fouling to settle over a full-service interval of five years. Any marine fouling will directly affect the energy efficiency of the hull, induce an increase in fuel consumption and subsequently a deterioration of the CII-rating. Hempel’s Hempaguard X7 coating delivers a guaranteed maximum average speed loss of 1.4 per cent over a service interval of 60 months (as defined by the ISO 19030 performance indicator “in-service performance”). This speed loss translates into 4.2 per cent fuel increase over a 60-month service interval.
Comparing the impact of coatings on the EEXI can easily be done by comparing two sister ships with identical surface preparation. Hempel assisted a tanker owner by comparing the fuel consumption at the same operational speed of the two vessels, one coated with Hempaguard and the other with another hull coating. The Hempaguard coated ship used considerably less fuel, showing fuel savings to far exceed 6 per cent.
Looking at a recent example that shows the potential savings that could be achieved, Hempel helped the owner of a cruise vessel to assess the performance of its Hempaguard X7 coating. Using our digital analysis tool SHAPE (Systems for Hull and Propeller Efficiency) it was calculated that with Hempaguard X7, the cruise ship’s fuel use increased by just 0.9 per cent over 60 months. This clearly shows that Hempaguard will keep the CII-rating under control throughout the service interval. A standard hull coating will experience a fuel consumption increase of around 18 per cent.
Taking only the CII-related fuel savings over 60 months into account there was an improvement of 17 per cent compared to a standard hull coating. Assuming a daily fuel consumption of around 40 tons, an overall activity level of 50 per cent and a bunker cost of USD 600 per ton, the savings generated by Hempaguard for the vessel owner were estimated to be around USD 3.7 million over 60 months.
The road ahead
Meeting the requirements of the IMO should not be the driving force to improve vessels’ carbon outputs. We must commit to a reduced-carbon future not for tick box reasons or financial gain, but as environmentally and socially responsible industries. Indeed, IMO’s work during June has been criticised in certain quarters who claim that adoption of the new MARPOL (International Convention for the Prevention of Pollution from Ships) amendments do not go far enough or fast enough.
Hempel is not waiting for legislation to force its hand. In line with our own ethics and to meet our customers’ expectations, in 2020 we introduced our sustainability framework called Futureproof through which we are building a sustainable growth programme for our business. Hempel’s five-year strategy calls for us to be carbon neutral in our own operations and have zero waste to landfill by 2025; to lay out an action plan to phase out hazardous raw materials; accelerate our efforts towards biocide-free products, and to halve the amount of scrapped finished goods and raw materials. This, in addition to introducing a water programme this year.
These reduction targets will be achieved alongside a programme of expansion as we grow our product range and market share. Sustainability and expansion must go hand in hand, and companies still relevant in five years’ time will today be aligning their operations for a low- or no-carbon future.
Source: Hempel, By Marcus Tullberg, Team Leader, Hull Performance, Group Segment Management, Hempel